Construction estimating is a critical process that determines the success of any project, from small residential builds to large commercial developments. Accurate estimates ensure that projects stay on budget, deadlines are met, and resources are allocated properly. However, even the most experienced estimators can make mistakes that lead to costly overruns, project delays, and frustrated clients.
In this blog, we will explore the 10 most common mistakes in construction estimating and provide practical tips on how to avoid them. By understanding these pitfalls, contractors and project managers can improve the accuracy of their estimates and ensure smoother project execution.
Inadequate Project Scope Definition
One of the most common mistakes in construction estimating is failing to define the project scope clearly. Without a clear and detailed scope of work, it’s impossible to create an accurate estimate. The project scope outlines the work to be completed, the materials needed, and the labor required. If these details are vague or incomplete, the estimate is likely to be inaccurate.
How to Avoid This Mistake:
Ensure that the project scope is clearly defined and thoroughly documented before starting the estimating process. Work closely with the client, architect, and other stakeholders to fully understand the project’s requirements. Break down the scope into specific tasks and ensure that nothing is overlooked.
Overlooking Indirect Costs
Indirect costs, such as permits, inspections, temporary utilities, and overheads, are often overlooked in construction estimates. While direct costs like materials and labor are easy to account for, indirect costs can be more difficult to calculate. Ignoring these expenses can lead to significant budget shortfalls.
How to Avoid This Mistake:
Take the time to identify and include all indirect costs in your estimate. These costs can vary depending on the location, project type, and regulatory environment, so be sure to consider all possible expenses. Use historical data and industry benchmarks to ensure accuracy when calculating indirect costs.
Relying on Outdated Data
Construction costs fluctuate over time, especially for materials like steel, lumber, and concrete. Using outdated pricing data when preparing an estimate can lead to inaccurate projections. If material prices have increased since your last project, your estimate will fall short of covering the actual costs.
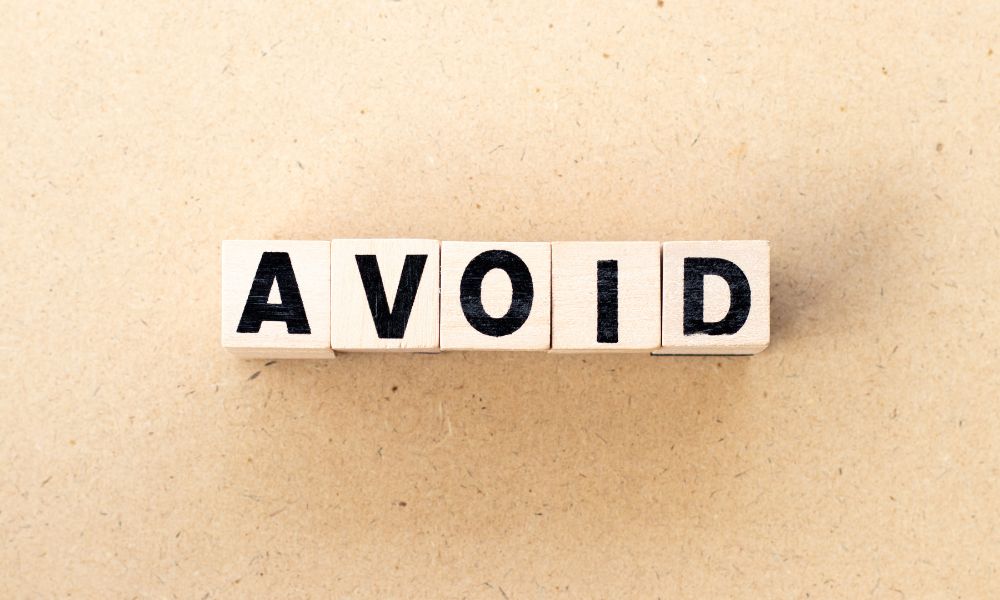
How to Avoid This Mistake:
Stay up-to-date with current market prices for materials and labor. Use real-time data and reliable sources to ensure that your estimates reflect current pricing. Many digital estimating tools offer access to up-to-date material costs, making it easier to avoid this mistake.
Underestimating Labor Costs
Labor costs are a major component of any construction project, yet they are often underestimated. This is especially true in areas with labor shortages or rising wages. Failing to account for all the labor needed to complete the project, including overtime or specialized labor, can lead to significant cost overruns.
How to Avoid This Mistake:
When estimating labor costs, be as specific as possible. Factor in the skill level of the workers, the number of hours required, and any potential overtime. Consider the availability of labor in your area and adjust your estimate accordingly. It’s also important to include costs for subcontractors and any additional labor needed to complete specialized tasks.
Neglecting Risk Management
Every construction project comes with risks, whether it’s weather delays, unforeseen site conditions, or material shortages. Many estimators fail to include contingency funds or consider these risks in their estimates, leaving the project vulnerable to unexpected expenses.
How to Avoid This Mistake:
Include a contingency allowance in your estimate to account for potential risks and uncertainties. This allowance can be a percentage of the total project cost, typically ranging from 5% to 10%. Additionally, conduct a thorough risk assessment during the planning phase to identify potential challenges and plan for them in advance.
Misjudging Project Timelines
Estimating the timeline of a construction project is just as important as estimating the costs. A common mistake is underestimating how long the project will take to complete, which can lead to rushed work, mistakes, and delays. Misjudging timelines can also result in higher labor costs as workers spend more time on-site than originally anticipated.
How to Avoid This Mistake:
Be realistic when estimating project timelines. Break the project down into phases and estimate the duration of each phase based on historical data and industry benchmarks. Account for any potential delays, such as bad weather, supply chain issues, or permitting holdups. A detailed project schedule will help ensure that your estimate is aligned with the project’s actual timeline.
Inaccurate Material Takeoffs
Material takeoffs involve calculating the quantities of materials needed for a project, and inaccuracies in this process can lead to wasted resources and higher costs. Ordering too much material results in excess inventory and wasted money, while ordering too little can cause project delays and additional costs for rush orders.
How to Avoid This Mistake:
Use digital takeoff tools like Bluebeam to improve the accuracy of your material takeoffs. These tools allow you to perform digital measurements directly from blueprints, ensuring precise calculations of materials. Double-check your takeoffs to ensure nothing is missed, and always account for waste, especially for materials like concrete or drywall.
Ignoring Permitting and Regulatory Requirements
Permitting and regulatory requirements can vary widely depending on the location and type of project. Failing to account for these requirements can lead to costly delays, fines, or even project shutdowns. Many estimators forget to include the time and cost associated with obtaining permits or complying with local regulations.
How to Avoid This Mistake:
Research the specific permitting and regulatory requirements for the project location during the estimating process. Include the cost of permits, inspections, and any necessary compliance measures in your estimate. Work with local authorities to ensure that all necessary approvals are in place before construction begins.
Failing to Account for Escalation
For long-term projects, material and labor costs are likely to rise over time. Failing to account for price escalation can lead to underestimating costs, especially for projects that take years to complete. Inflation, supply chain disruptions, and labor shortages can all drive up prices, and ignoring this factor can leave the project underfunded.
How to Avoid This Mistake:
Include an escalation factor in your estimate for projects with long timelines. This factor can be based on historical inflation rates or current market trends. For larger projects, consider including an escalation clause in your contract that allows for adjustments in material and labor costs as they fluctuate over time.
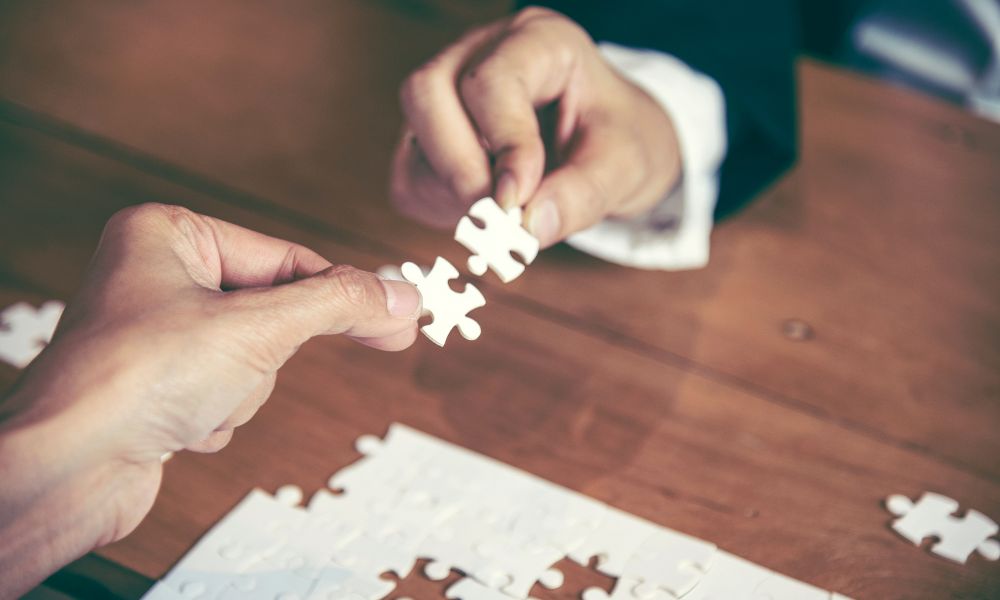
Lack of Communication with Stakeholders
Poor communication between the estimator, project manager, client, and subcontractors can lead to misunderstandings and incorrect estimates. If the estimator doesn’t fully understand the client’s vision or the project manager’s approach, critical details may be missed in the estimate.
How to Avoid This Mistake:
Establish clear lines of communication between all stakeholders involved in the project. Hold regular meetings to discuss the project’s scope, budget, and timeline. Ensure that everyone has access to the same information and that any changes are communicated promptly. Collaboration and transparency are key to preventing costly mistakes in the estimating process.
How Measure Manage Can Help You Avoid Common Estimating Mistakes
At Measure Manage, we understand the complexities of construction estimating and the importance of avoiding costly mistakes. Our team of experienced estimators uses advanced tools like Bluebeam and Excel to ensure that every estimate is accurate, comprehensive, and based on the latest data. We work closely with clients to define the project scope, identify potential risks, and provide a detailed estimate that sets the foundation for project success.
As members of the Royal Institute of Chartered Surveyors (RICS) and the Australian Institute of Quantity Surveyors (AIQS), we follow industry best practices and adhere to the highest standards of professionalism. Whether you’re working on a residential, commercial, or civil project, Measure Manage can help you avoid common estimating mistakes and ensure a smooth, successful construction process.
Ready to Get Your Estimate Right?
Don’t let common estimating mistakes derail your project. Contact Measure Manage today to request a quote or learn more about our professional estimating services. Visit our website, call us, or fill out our online form to get in touch with our expert team.